Overview
At Howrah Ferrous, we strictly follow the environmental standards in our manufacturing units and do not allow any activity that may affect the environment. Our company takes every measure to control its business activities that might have a nagetive impact on the environment.
- As protecting our surroundings is one of our principal responsibilities, we take proactive measures to promote environmental protection.
- By educating our clients as well as influencing them, we aim to create an eco-frinedly working culture around us.
- We ensure there is a mutual agreement between us and our partners regarding any environmental issues that may occur.
Manufacturing Units
Manufacturing Process
At Howrah Ferrous Limited, all products are manufactured according to worldwide standards. Here products are tested as per the required respective standard and we ensure that we deliver quality. We have fully developed in-house facilities for sand, raw materials testing, chemical analysis, load testing, and other quality control measures. Beginning from the incoming material and production to the quality testing and dispatching of products, every stage of our product manufacturing process is monitored by our expert team of production managers. Spectrometers are being used in our system to determine results with more accuracy.
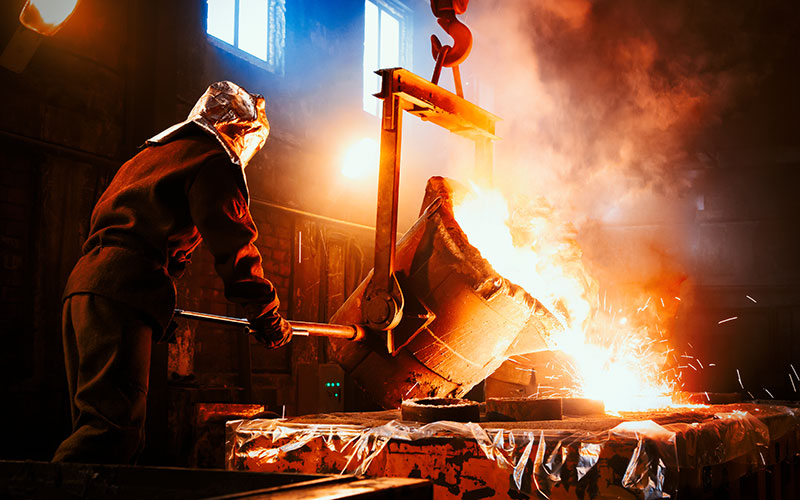
- VMC pattern shop
- Melting
- Molding line
Production Facilities
We merge our in-house design with our VMC Machines to produce patterns within a short span of time. Our products are designed with the help of AutoCAD, Creo Parametric and Solidworks software and optimized through a series of simulations. One 4 axis VMC machine is being used to produce fresh designs with greater speed and perfection. Our company has a melting capacity of 22,500 tons per year of ductile iron using 4 induction furnaces with a finished goods capacity of 12,000 tons. We produce GGG50 Grade of Ductile iron.
Manufacturing Facilities
At Calcutta Export Company, the products are manufactured in accordance with the relevant international market standards.
SAND PLANT
- RMC-15 Sand Plant with Capacity of 15 Ton Per Hour for 900 M/C
- RMC-20 Sand Plant with Capacity of 20 Ton Per Hour for SF M/C
- IRM-600 Sand Plant with Capacity of 15 Ton Per Hour for 450 M/C
- IRM-300 Sand Plant with Capacity of 9 Ton Per Hour for Hand Mould
- Online Sand Testing Available in the above machine.
MELTING SYSTEM
- One No. One Ton Induction Furnace with 2 Nos. 1000Kg Crucible with 750 Kw power pack.
- One No. One Ton Induction Furnace with 1 Nos. 1000Kg Crucible with 750 Kw power pack.
- One No. One Ton Induction Furnace with 1 Nos. 1000Kg Crucible with 1000 Kw power pack.
CORE MAKING
- Three Nos. Cold Box Core Shooter (3Kg, 3Kg, & 7 Kg.)
- Three Nos. 50 Kg Core Sand Mixer
- AIR Receiver Horizontal for CO2
- Electrically Heated Core Oven
MOULDING SYSTEM
- SMFA 900 Moulding Machine (Jolt Squeeze)
- SMFA 900 Moulding Machine MHS System
- ARPA-450 Moulding Machine (Jolt Squeeze)
METAL POURING
- Mechanical Pouring through the hoist.
- Hand Pouring facility also available.
SHOT BLASTING
- 500 Kg batch capacity shot blasting machine for surface cleaning of the casting, fitted with a dust collector.
PAINT FACILITY
- Paint shop for Epoxy/enamel paint up to 500 microns
- Bitumen painting also available through dipping or spraying process.
- DFT checking done through Elcometer.
- Adhesion/Pull off testing/Scratch hardness testing facility available.
- Viscosity check by B4 cup before painting.
CNC Machine System
Flat bed type CNC Turning Machine up to 1200mm dia.
- Twelve Nos. Turning Machine (4 Nos. CNC & 8 Nos. Manual)
- Twelve Nos. Drilling Machine (2 Nos. CNC & 10 Nos. Manual)
- Three Nos. shaper machine
- One Universal Tapping Machine
- One Table & One Tool grinding Machine
Process Flow Chart
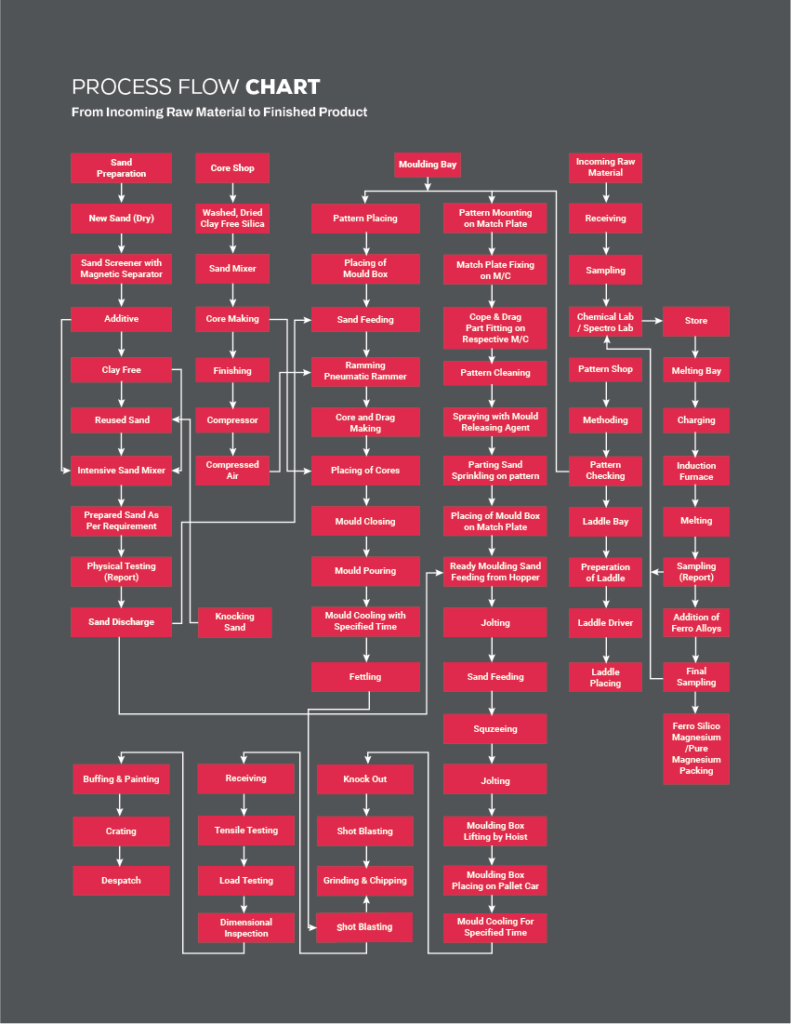